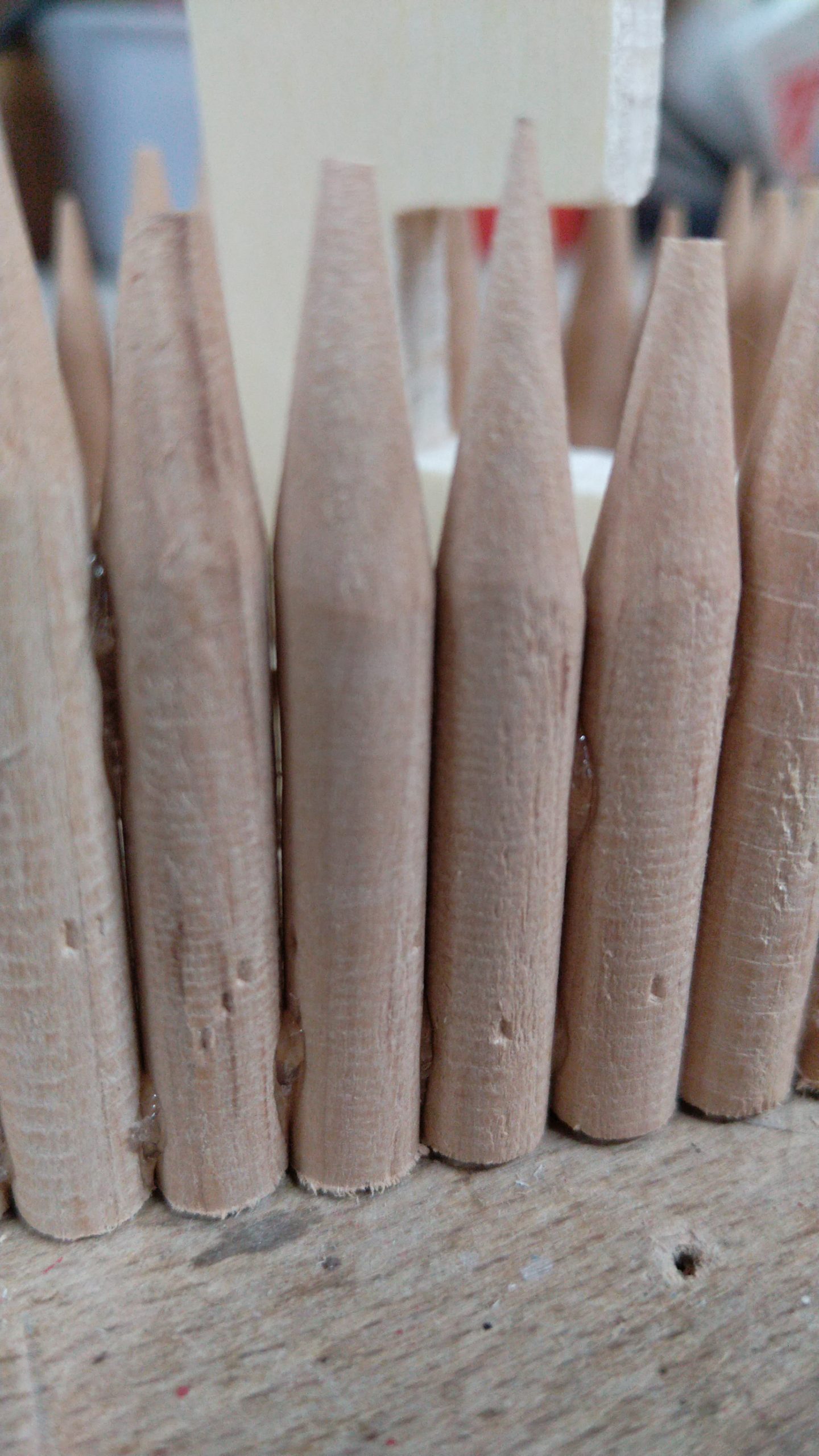
How to Make Your own Wood Dowels
Dowels – round, long pieces – are a very versatile administration form of wood. They have their use in fine woodworking as well as crafting. And the best part? You can easily make your own! What are Wood Dowels good for? Since the grain runs along their axis they are… Continue Reading How to Make Your own Wood Dowels